Polymer Screen Changer are established in the plastics industry since decades. Due to its reliable twin-piston design, they offer a continuously production and there is no production stop needed for screen change. Each of both pistons is usually equipped with circular shaped (see attmt. 1) screen packs, depending on the application with a filter fineness between 20µm and 200µm. Therefore this units guaranty a high quality and clean polymer melt for any extrusion, compounding or recycling application. Depending on the filter fineness and contamination level of the polymer, after a few hours or days the screen packs needs to be changed, as the pressure has rised because the screens are clogged with the collected contamination particles. For screen change the operator then moves one piston at a time with a simple hydraulic cylinder out of the screen changer housing, to replace the contaminated screen with a new one. This procedure takes a few minutes, while the polymer still flows continuously through the remaining piston in the housing. Once the screen of the first piston is changed and this piston has moved back in the filter housing, this procedure is repeated with the second piston, to have finally both new screens in the production line.
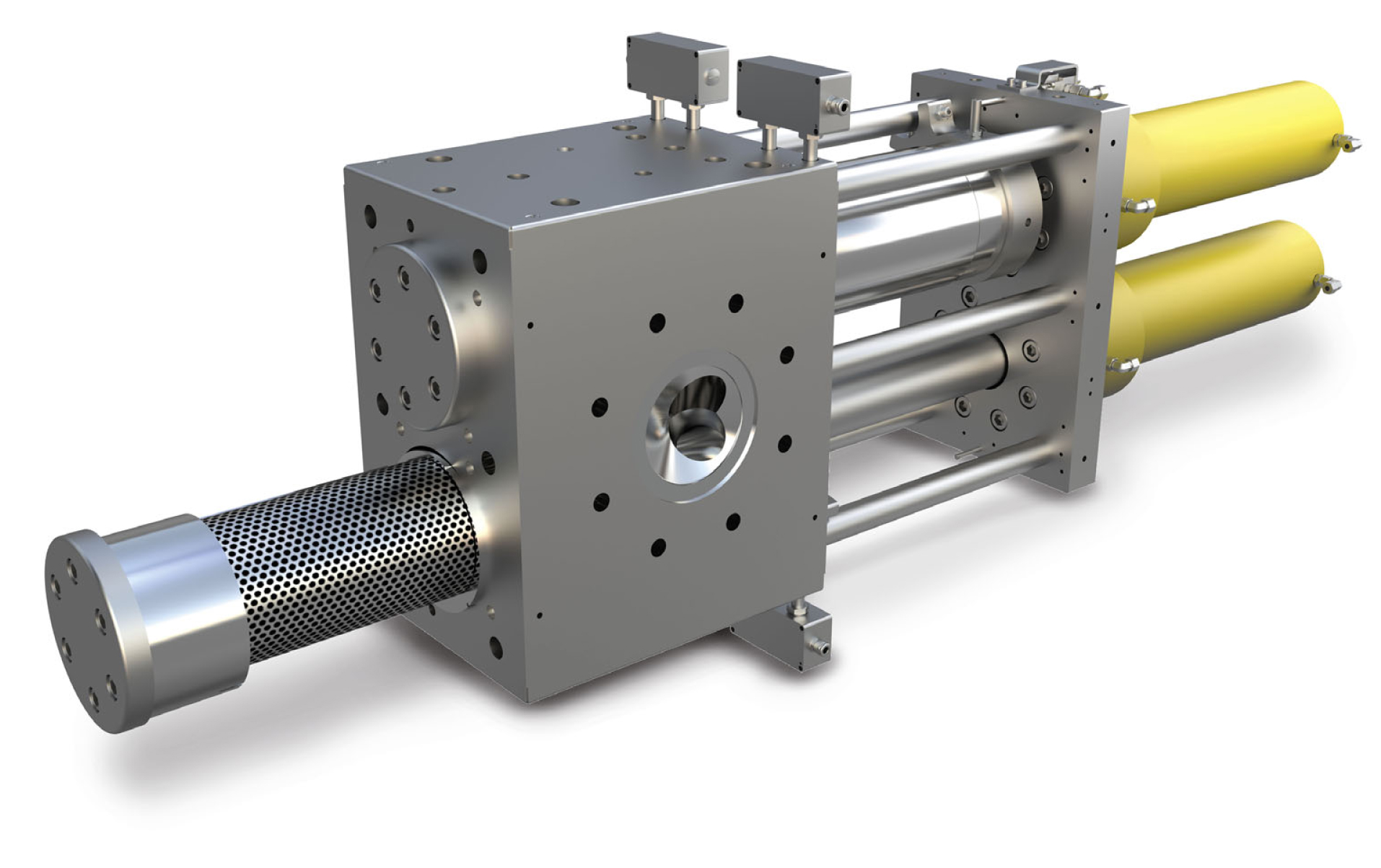